By Krosino | 16 March 2023 | 0 Comments
What do you need know about carbon fiber processing in Krosino?
CARBON FIBER PROCESSING
There are many carbon fiber manufacturing methods, and each has its advantages and disadvantages. The four most common methods: wet layup, pultrusion, prepreg layup, and vacuum-assisted resin transfer molding (VARTM).
Carbon fiber is made of thin, strong crystalline filaments of carbon that is used to strengthen material. Carbon fiber can be thinner than a strand of human hair and gets its strength when twisted together like yarn. Then it can be woven together to form cloth and if needed to take a permanent shape, carbon fiber can be laid over a mold and coated in resin or plastic.
An Overview of The Carbon Fiber Manufacturing Process:
Carbon fiber is made from a process that is part chemical and part mechanical. It starts by drawing long strands of fibers and then heating them to a very high temperature without allowing contact to oxygen to prevent the fibers from burning. This is when the carbonization takes place, which is when the atoms inside of the fibers vibrate violently, expelling most of the non-carbon atoms. This leaves a fiber composed of long, tightly inter-locked chains of carbon atoms with only a few non-carbon atoms remaining.
A typical sequences used to form carbon fibers from polyacrylonitrile involves spinning, stabilizing, carbonizing, treating the surface and sizing.
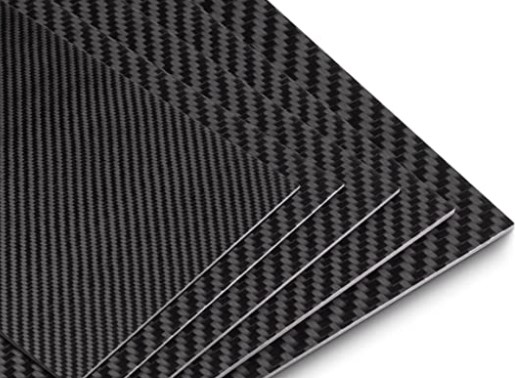
Advantages&Application
of Carbon Fiber
ADVANTAGE:
> Lasting Performance > Good Resilience > High Strength > Good Tenacity > High Corrosion Resistance > Excellent Structural Properties > UV Resistant Inhibited > Environmentally Safe > Variety Of Colors For Choice > Non-Magnetic Electromagnetic > Consistent Cross Section > Dimensional Stability > Non-Conductive Thermally And Electrically > Wide Temperature Range Use > Superior Dimensional Stability > Smooth finish on surface
APPLICATION:
Almost anything. Because of its special characteristics, carbon fiber is very popular in many industries such as aerospace, automotive, military, and recreational applications:
>Loudspeakers for Hi-fi equipment, pickup arms, robot arms,Audio equipment
>Aerospace, road and marine transport, sporting goods,bikes
>Large generator retaining rings, radiological equipment
>Missiles, aircraft brakes, aerospace antenna and support structure, large telescopes, optical benches, waveguides for stable high-frequency, precision measurement frames
>genera engineering,Textile machinery, etc.
>Automobile hoods, novel tooling, casings and bases for electronic equipments, EMI and RF shielding, brushes
>Chemical industry; nuclear field; valves, seals, and pump components in process plants
>Medical applications in prostheses, surgery and x-ray equipment, implants, tendon/ligament repair
of Carbon Fiber
ADVANTAGE:
> Lasting Performance > Good Resilience > High Strength > Good Tenacity > High Corrosion Resistance > Excellent Structural Properties > UV Resistant Inhibited > Environmentally Safe > Variety Of Colors For Choice > Non-Magnetic Electromagnetic > Consistent Cross Section > Dimensional Stability > Non-Conductive Thermally And Electrically > Wide Temperature Range Use > Superior Dimensional Stability > Smooth finish on surface
APPLICATION:
Almost anything. Because of its special characteristics, carbon fiber is very popular in many industries such as aerospace, automotive, military, and recreational applications:
>Loudspeakers for Hi-fi equipment, pickup arms, robot arms,Audio equipment
>Aerospace, road and marine transport, sporting goods,bikes
>Large generator retaining rings, radiological equipment
>Missiles, aircraft brakes, aerospace antenna and support structure, large telescopes, optical benches, waveguides for stable high-frequency, precision measurement frames
>genera engineering,Textile machinery, etc.
>Automobile hoods, novel tooling, casings and bases for electronic equipments, EMI and RF shielding, brushes
>Chemical industry; nuclear field; valves, seals, and pump components in process plants
>Medical applications in prostheses, surgery and x-ray equipment, implants, tendon/ligament repair
What Is Carbon Fiber?
When selecting a material, consider the material properties, manufacturability characteristics, cosmetic appearance, and cost.
Carbon fiber is a super-strong yet lightweight material. It is five times stronger than steel, twice as stiff and around 1.5 times lighter.
Carbon Fiber is a polymer and is sometimes known as graphite fiber. It is a very strong material that is also very lightweight. Carbon fiber is five-times stronger than steel and twice as stiff. Though carbon fiber is stronger and stiffer than steel, it is lighter than steel; making it the ideal manufacturing material for many parts. These are just a few reasons why carbon fiber is favored by engineers and designers for manufacturing.
Fibers are bundled in various sizes designated in thousands (K) of fibers. 1K, 3K, 6K, 12K, 24K, 50K and others are common bundle sizes. These fibers are woven into fabric with various weave patterns. 3K fabric is most common. The various types of fiber will have the same “K” designation to indicate the number of fibers in the bundle. These numbers describe the size of the bundle used and have little to do with the quality of the fiber itself.
Carbon Fiber Plate Making and Post Processing
1. Cutting the prepreg: According to the requirements of the drawings, cut the carbon fiber prepreg into the appropriate length and width, usually the thickness of the prepreg is about 0.2mm, and then cut the corresponding amount of carbon fiber prepreg according to the thickness of the carbon fiber plate.
Carbon Fiber Plate Making and Post Processing
Carbon fiber plate is the carbon fiber arranged in the same direction using resin infiltration hardening to form carbon fiber plate, can effectively solve the problem of multi-layer carbon fiber distribution work difficulty and large amount of engineering, good reinforcement effect, convenient construction.
Carbon fiber plates are mostly made of carbon fiber composite prepregs. If you want to produce carbon fiber plates for composite needs, the raw materials should be selected well, and then the production process depends on it.
1. Cutting the prepreg: According to the requirements of the drawings, cut the carbon fiber prepreg into the appropriate length and width, usually the thickness of the prepreg is about 0.2mm, and then cut the corresponding amount of carbon fiber prepreg according to the thickness of the carbon fiber plate.
2. prepreg layering: the size is appropriate, the amount is appropriate, the next is the carbon fiber plate production process in one of the most important links, it is the layering. Prepregs need to be stacked in different directions so that the positive pressure in different directions remains the same. There are usually 0°, ±30°, ±45° and 90° to choose from, and the layup is usually carried out in the way of mixed layup.
3. high temperature curing molding: carbon fiber prepreg layer is finished, just have the prototype of carbon fiber plate, but also need to put it into the autoclave high temperature curing molding, this time the carbon fiber plate has been basically shaped. Different materials of carbon fiber prepreg need to choose different temperature, pressure and time.
4. Grinding treatment: Take out the carbon fiber plate from the autoclast, cut the excess part of the edge, polish the surface, remove impurities and dirt, and keep the surface smooth and clean.
Carbon fiber plate after curing, in order to precision requirements or assembly needs, it still need to be cutting, drilling and other post-processing. In the same cutting process parameters, cutting depth and other conditions, the selection of different materials, size, shape of the cutting tool and drilling tool, the effect is very different, at the same time, the strength of the cutting tool and drilling tool, direction, time and temperature and other factors will also affect the processing results.
In the process of post-machining, try to choose the sharp tool with diamond coating and the drill bit with integral hard alloy. The wear resistance of the tool and the drill itself determines the quality of machining and the service life of the tool. If the cutting tool and drill are not sharp enough or used improperly, it will not only accelerate the wear and increase the processing cost of the product, but also cause damage to the board, affecting the shape and size of the board and the stability of the size of the holes and slots on the board. In serious cases, it will cause lamellar tearing of the material or even block collapse, leading to the scrapping of the whole board.
When drilling carbon fiber sheets, we need make the speed as faster as we can. In terms of bit selection, the PCD8 bit's unique tip design is suitable for carbon fiber sheet and can penetrate carbon fiber sheet better, reducing the risk of delamination.
When cutting the thick carbon fiber sheet, it is recommended to use the left and right spiral edge design of double-edge compression milling cutter, the sharp cutting edge has the upper and lower spiral tip at the same time, the cutting balance tool up and down axial force, to ensure that the cutting force is directed to the inside of the material, to obtain stable cutting conditions, can inhibit the material stratification phenomenon.
Leave a Reply
Your email address will not be published.Required fields are marked. *
CATEGORIES