By Krosino | 16 March 2023 | 0 Comments
What do you know about CNC Machining Service ?
CNC Machining Services
CNC Machining refers to a process of machining parts on CNC machine. Machining procedures of CNC machine are generally consistent with those of traditional machine tools, but there are obvious changes after machining. Machining method using digital information to control the displacement of parts and tools. It is an effective way to solve the problems of variable parts variety, small batch, complex shape and high precision, and to realize high efficiency and automatic processing.
The initial idea of CNC machine tools, in 1952, the Massachusetts Institute of Technology developed a three-dimensional CNC milling machine. In the mid-1950s this kind of CNC milling machine had been used to process aircraft parts. In the 1960s, CNC system and programming work increasingly mature and perfect, CNC machine tools have been used in various industrial sectors, but the aerospace industry has always been the largest user of CNC machine tools. Some large aviation factories are equipped with hundreds of CNC machine tools, mainly cutting machines. CNC machining parts include aircraft and rocket integral panel, girder, skin, spacer frame, propeller, aero-engine casing, shaft, disc, blade mold cavity and liquid rocket engine combustion chamber special cavity surface. CNC machine tools at the beginning of development is based on continuous trajectory of CNC machine tools, continuous trajectory control.
Continuous trajectory control, also known as contour control, requires the tool to move relative to the parts according to the specified trajectory. After the development of point control CNC machine tools. Point control means that the tool moves from one point to another, as long as it reaches the target accurately at the end, regardless of the path of movement.
Continuous trajectory control, also known as contour control, requires the tool to move relative to the parts according to the specified trajectory. After the development of point control CNC machine tools. Point control means that the tool moves from one point to another, as long as it reaches the target accurately at the end, regardless of the path of movement.
Process analysis
CNC machining of the parts involved a wide range of issues, the following combined with the possibility and convenience of programming put forward some must be analyzed and examined.
1, the size should be in line with the characteristics of CNC machining
In NC programming, the dimensions and positions of all points, lines and surfaces are based on the programming origin. Therefore, it is best to directly give the coordinate size on the part drawing, or try to quote the size with the same reference.
In NC programming, the dimensions and positions of all points, lines and surfaces are based on the programming origin. Therefore, it is best to directly give the coordinate size on the part drawing, or try to quote the size with the same reference.
2. The conditions of geometric elements should be complete and accurate
In the process of programming, the programmer must fully grasp the geometric parameters and the relationship between the geometric elements that constitute the contour of the parts. Because all geometric elements of the parts contour should be defined in automatic programming, and the coordinates of each node should be calculated in manual programming, no matter which point is not clear or uncertain, programming can not be carried out. However, due to the part design personnel in the design process is not considered or ignored, often appear parameters incomplete or unclear, such as arc and straight line, arc and arc is tangent or intersect or separate. So in the review and analysis of drawings, must be careful, found problems in a timely contact with the designer.
In the process of programming, the programmer must fully grasp the geometric parameters and the relationship between the geometric elements that constitute the contour of the parts. Because all geometric elements of the parts contour should be defined in automatic programming, and the coordinates of each node should be calculated in manual programming, no matter which point is not clear or uncertain, programming can not be carried out. However, due to the part design personnel in the design process is not considered or ignored, often appear parameters incomplete or unclear, such as arc and straight line, arc and arc is tangent or intersect or separate. So in the review and analysis of drawings, must be careful, found problems in a timely contact with the designer.
3, reliable positioning reference
In numerical control machining, machining process is often more concentrated, with the same datum positioning is very important. Therefore, it is often necessary to set some auxiliary reference, or add some process boss to the blank.
In numerical control machining, machining process is often more concentrated, with the same datum positioning is very important. Therefore, it is often necessary to set some auxiliary reference, or add some process boss to the blank.
4, unified geometric type or size
It is best to adopt uniform geometric type or size for the shape and inner cavity of parts, which can reduce the number of tool changes, and may also apply control procedures or special procedures to shorten the length of the program. The shape of the parts is as symmetrical as possible, which is convenient to use the mirror machining function of the CNC machine tool to program, so as to save programming time.
It is best to adopt uniform geometric type or size for the shape and inner cavity of parts, which can reduce the number of tool changes, and may also apply control procedures or special procedures to shorten the length of the program. The shape of the parts is as symmetrical as possible, which is convenient to use the mirror machining function of the CNC machine tool to program, so as to save programming time.
Part clamping
First, the basic principles of positioning and installation
When machining parts on CNC machine tools, the basic principle of positioning installation is reasonable choice of positioning datum and clamping scheme. The following points should be noted in the selection:
1. Strive to unify the benchmark of design, process and programming calculation.
2, as far as possible to reduce the number of clamping, as far as possible after a positioning clamping, processing all the surface to be processed.
3, avoid using manual adjustment machining scheme, in order to give full play to the effectiveness of CNC machine tools.
Second, the basic principle of selecting fixtures
The characteristics of CNC machining put forward two basic requirements to the fixture: one is to ensure that the coordinate direction of the fixture and the coordinate direction of the machine is relatively fixed; The second is to coordinate the size of the parts and the machine coordinate system. In addition, consider the following:
1, when the parts processing batch is not large, should try to use the combination of fixture, adjustable fixture and other general fixture, in order to shorten the production preparation time, save production costs.
2, in the mass production to consider the use of special fixture, and strive for simple structure.
3. The loading and unloading of parts should be fast, convenient and reliable to shorten the pause time of the machine tool.
4. The parts on the fixture should not interfere with the machining of the surface of the parts, that is, the fixture should be open, and the positioning and clamping mechanism components should not affect the cutting tool in the processing (such as collision, etc.).
Machining error
CNC machining errors are formed by programming errors, machine errors, positioning errors, tool errors and other errors
Among them:
1. Programming error is composed of approximation error and rounding error. The approximation error is generated in the process of approximating a non - circular curve with a straight or circular segment. The rounding error is the error caused by rounding the coordinate value to the integer pulse value during data processing. Pulse equivalent refers to the displacement of each unit pulse corresponding to the coordinate axis. For ordinary precision CNC machine tools, the general pulse value is 0.01mm; More precise CNC machine tools pulse when the value is 0.005mm or 0.001mm, etc.
2. Machine tool error is caused by CNC system error, feed system error and other reasons.
3. Positioning error is generated when the workpiece is positioned on the fixture and the fixture is positioned on the machine tool.
4. The tool error is generated when determining the relative position of the tool and the workpiece.
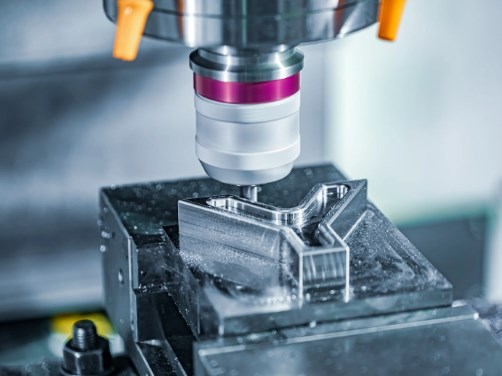
CNC MILLING
CNC milling is a subtractive manufacturing method that uses a cutting tool to moves and rotate to remove material. CNC mills can be used for cutting and machining operations of various plastic and metal materials. It is suitable for any industry that requires precision components and is also an ideal tool for making molds.
LEARN MORE about CNC MILLING
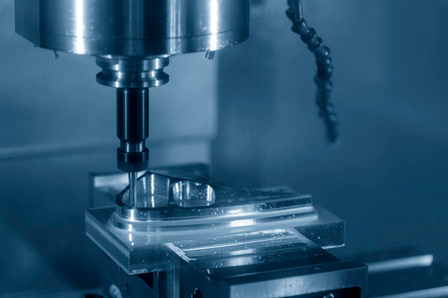
LASER CUTTING
a thermal process in which a focused laser beam is used to melt material in a localised area. A co-axial gas jet is used to eject the molten material and create a kerf. A continuous cut is produced by moving the laser beam or workpiece under CNC control.
Read more
Read more
CNC TURNING
CNC turning removes material by contacting a cutter with the high-speed rotating workpiece and is usually used to create round or tubular shapes. The CNC turning process allows the generation of complex external geometries and internal holes, including the machining of various threads.
LEARN MORE ABOUT CNC turning
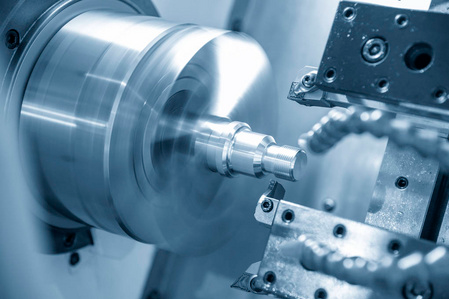
SHEET METAL
Sheet metal processing is called sheet metal processing. For example, the use of plate to make chimneys, iron drums, fuel tank pots, ventilation pipes, elbows,advertising word ,computer Chassis,Machine cover panel and so on.The main procedures are shearing, bending buckle edge, bending molding, welding, riveting and so on, which requires certain geometric knowledge. Sheet metal parts are thin plate hardware parts, that is, parts that can be machined by stamping, bending, drawing and so on.
LEARN MORE ABOUT CNC turning
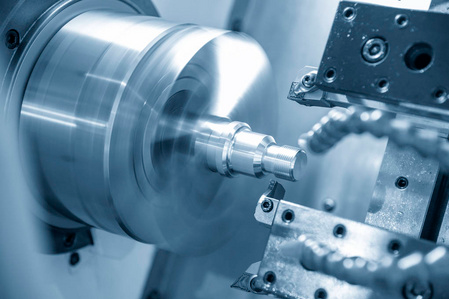
SHEET METAL
Sheet metal processing is called sheet metal processing. For example, the use of plate to make chimneys, iron drums, fuel tank pots, ventilation pipes, elbows,advertising word ,computer Chassis,Machine cover panel and so on.The main procedures are shearing, bending buckle edge, bending molding, welding, riveting and so on, which requires certain geometric knowledge. Sheet metal parts are thin plate hardware parts, that is, parts that can be machined by stamping, bending, drawing and so on.
READ MORE
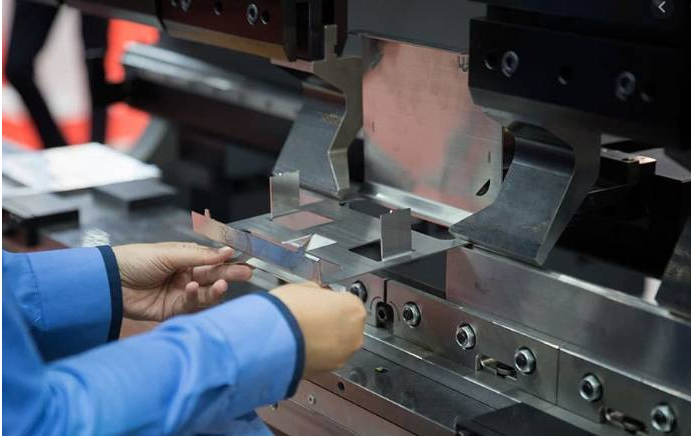
CNC Machining Materials & Finishes
There are a wide variety of materials that can be machined using CNC technology, KROSINO provides CNC machining quotes for more than 25 kinds of materials. In terms of finishes, various types of surface finishes can be applied to CNC machined parts.
-Metal: Aluminum, Steel, Stainless Steel, Brass, Bronze, Titanium Alloy, Zinc Alloy.
-Carbon fiber:T300,T600,T700,T800 and T1000.
-Plastic: POM(Acetal / Delrin),ABS, PC, PMMA(Acrylic), PA(Nylon), PP, PVC, HDPE, PPS, PEEK.
-Finishes: We support one-stop CNC machining surface finishing to meet the visual and functional requirements of any design. Including sandblasting, anodizing,laser engraving,mirror polishing, painting, printing, laser etching, electroplating, powder coating, etc.
|CNC Metal Machining
Whether it is prototypes or end-use parts, our mastery of CNC metal machining techniques helps us to achieve tighter tolerances, faster turnaround times, and more challenging manufacturing projects.
PRODUCTS DISPLAY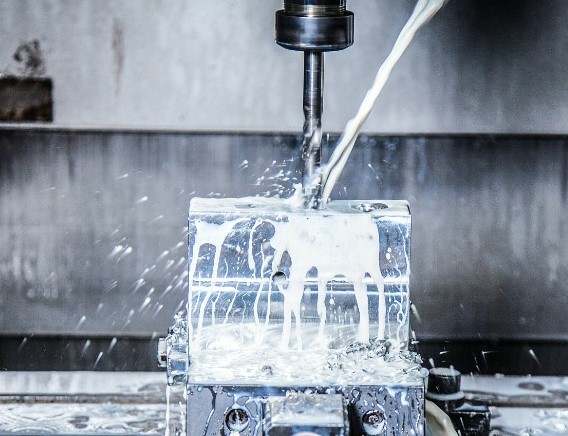
PRODUCTS DISPLAY
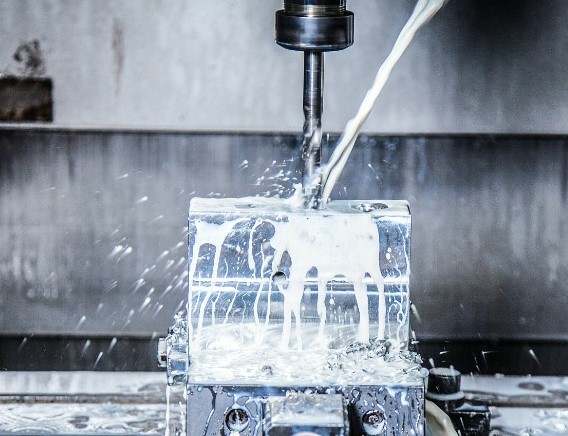
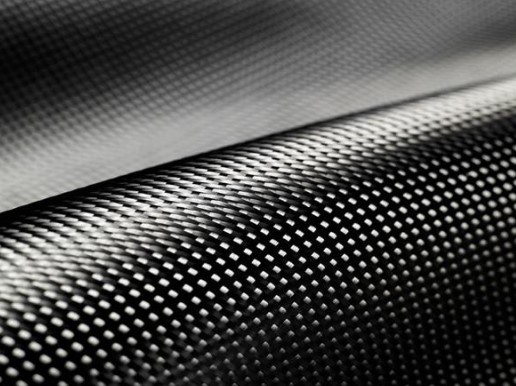
|CNC Carbon Fiber Machining
Carbon fiber material is very common used in recent years.
Krosino have cnc engraving and milling machine,heat press machine cutting machine,
molding machine and shearing machine that could supply different kinds of carbon fiber material
to process your parts such as drones frame panel,automative machine board,car board.PRODUCTS DISPLAY
Krosino have cnc engraving and milling machine,heat press machine cutting machine,
molding machine and shearing machine that could supply different kinds of carbon fiber material
to process your parts such as drones frame panel,automative machine board,car board.PRODUCTS DISPLAY
|CNC Plastic Machining
A variety of engineering-grade materials can be used for CNC plastic machining. The machined plastic parts are 100% functional and able to be mechanically tested.
PRODUCTS DISPLAY
PRODUCTS DISPLAY
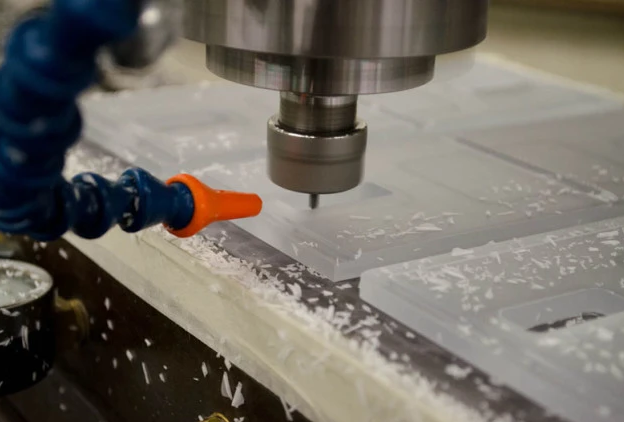
Leave a Reply
Your email address will not be published.Required fields are marked. *
CATEGORIES